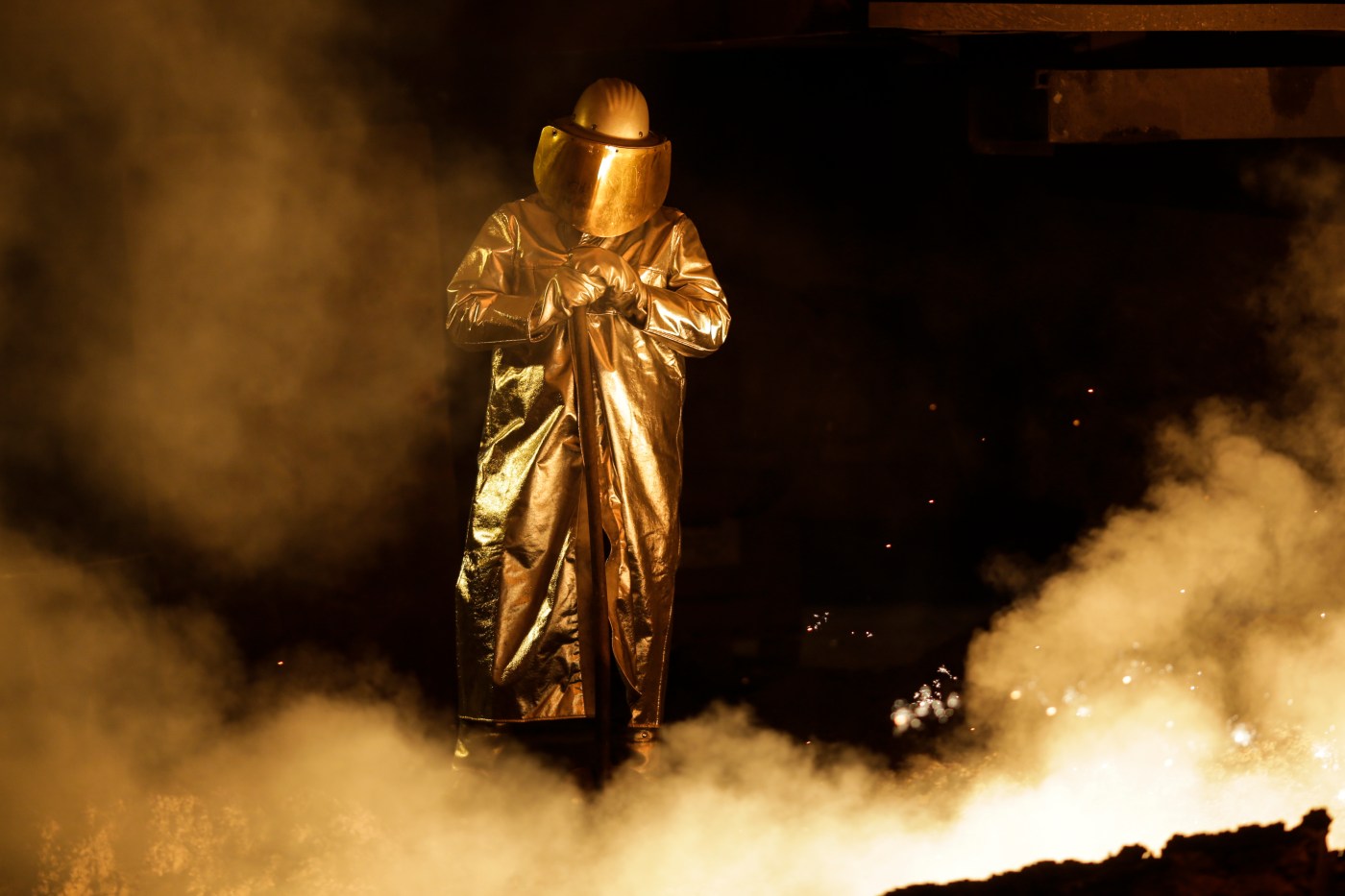
Can steelmaking be made climate friendly?
The U.S. Department of Energy awarded nearly $1.5 million to the University of Minnesota’s Natural Resources Research Institute to develop carbon-free methods of readying iron mined in the state for steelmaking.
NRRI, which has labs in Hermantown and Coleraine, received $575,000 as part of a $2.8 million grant to work with the University of Minnesota to develop a microwave hydrogen plasma process to replace blast furnaces. It also received $900,000 as part of a $3 million grant to work with Tufts University in Medford, Mass., to develop a method to directly reduce iron ore concentrates with ammonia.
Both processes would eliminate carbon emissions from that step in the steelmaking process. Reduction of greenhouse gases, namely carbon dioxide, is key in slowing or preventing the worst effects of a warming climate.
The global steelmaking industry accounted for approximately 7% of carbon dioxide emissions in 2020, according to the U.S. Energy Information Administration.
“It’s a huge amount of greenhouse gas emissions from just iron and steel alone,” said Matt Mlinar, research group leader for minerals processing and metallurgy at NRRI. “They (the Department of Energy) are trying to look for alternative ways to produce the same products while not emitting CO2.”
Both methods the NRRI will help research replace carbon with hydrogen, either through the microwave hydrogen plasma process or with ammonia, which is a nitrogen and hydrogen compound.
Typically, coal or natural gas is used to remove oxygen from iron before a traditional oxygen furnace or, increasingly, an electric arc furnace converts it to steel.
Carbon monoxide in fossil fuels can pick an oxygen atom off the iron oxide, removing it from the iron but forming carbon dioxide and other gases as a byproduct. Those gases are then released into the atmosphere. But if hydrogen is used instead, two hydrogen atoms can bond with one oxygen atom from the iron oxide and form water, and water vapor is a far more desirable byproduct than greenhouse gases.
“We want hydrogen to do the reduction, and not the CO (carbon monoxide) because then the CO2 (carbon dioxide) will form, and herein lies the problem,” said Brett Apigarelli, a senior research scientist at NRRI.
The projects were part of $28 million in funding announced last week by the Department of Energy’s Advanced Research Projects Agency-Energy, or ARPA-E, under the Revolutionizing Ore to Steel Impact Emissions, or ROSIE, program.
“Iron and steel production are among the most difficult industrial sectors to decarbonize, which is why ARPA-E is laser focused on accelerating game-changing technological breakthroughs to lower emissions from these critical sectors,” ARPA-E director Evelyn N. Wang said in a news release. “Today’s announcement will help the nation achieve President Biden’s ambitious clean energy and net-zero goals while also reinforcing America’s global leadership in clean manufacturing for generations to come.”
Separately, the NRRI last year received a $2.1 million grant from the Department of Energy to study different lower-carbon technologies for the iron and steel industries. That includes using biochar, wood heated to a high temperature in a low-oxygen setting, to replace coal in the steelmaking process.
Mlinar said ARPA-E, which is funding the hydrogen projects, is known for backing “moonshot” research.
“They fund a lot of really, really high-risk, high-reward projects that otherwise it’s hard to get funding for,” Mlinar said.
Eric Enberg, a volunteer for the Northland Chapter of the Citizens’ Climate Lobby, said carbon dioxide emissions from the iron ore and steelmaking industries were long considered difficult to abate.
But that’s changing.
“How do we ever decarbonize these things?” Enberg said. “Well, it’s turning out that it’s a lot easier than we thought. There’s a lot of things we can do — not as cheaply perhaps right now versus carbon-based fuels.”
Enberg said federal funding could help ideas advance beyond the so-called “valley of death” when new technologies under development putter out.
Citizens Climate Lobby has also been arguing for a price on carbon. Enberg if the industry sees traditional carbon-intensive methods and processes becoming cost-prohibitive, it could spur them to adopt lower-carbon or carbon-free processes.
“You need to have the push and the pull,” Enberg said.
If the hydrogen processes work, and are then scaled up, they could transform the state’s iron mining industry again.
First, high-grade was mined, and it could be added directly to a blast furnace. When that was depleted, processing lower-grade ores into concentrated pellets became the norm.
But lower-carbon or carbon-free methods could take pellets out of the equation.
Enberg said the industry should be quick to adopt new technologies in Minnesota because if pellets aren’t needed, there’s nothing stopping ore mined on the Iron Range from being shipped out of state for processing somewhere else.
“We really need to take advantage of this opportunity; otherwise, it’s going to be gone,” Enberg said. “And if it’s gone, then the Iron Range is going to be stuck with the technology from the last century. It will not have moved forward, and the technology and the jobs and all that are going to be somewhere else.”