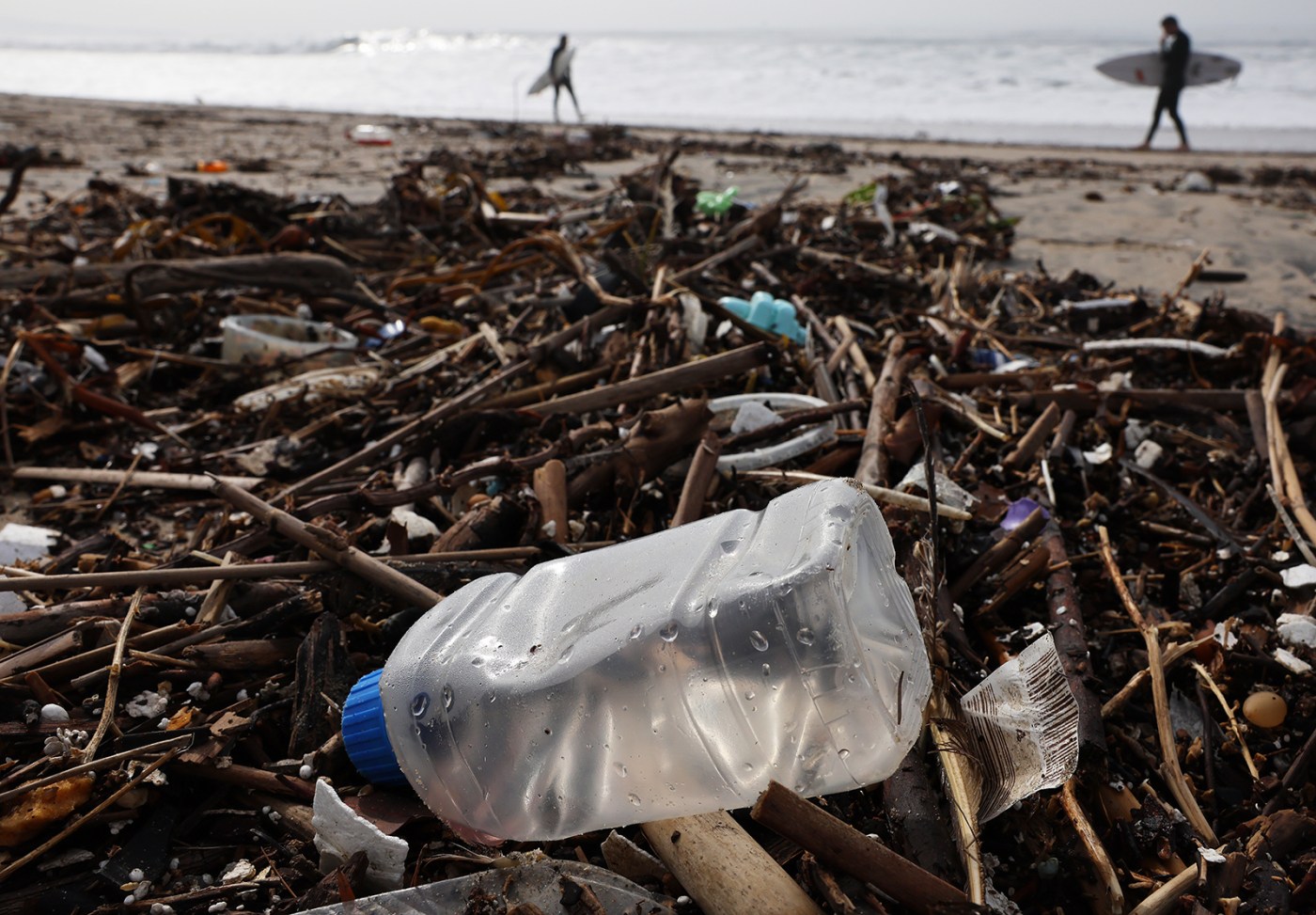
Has a California lab discovered the holy grail of plastic recycling?
Susanne Rust | Los Angeles Times (TNS)
Despite the planet’s growing plastic pollution crisis, petroleum-based polymers have become an integral part of modern life. They make cars and airplanes lighter and more energy efficient. They constitute a core material of modern medicine by helping to keep equipment sterile, deliver medicines and build prosthetics, among many other things. And they are a critical component of the wiring and hardware that underlies our technology-driven civilization.
The trouble is, when they outlive their usefulness, they become waste and end up polluting our oceans, rivers, soils and bodies.
But new research from a team of chemists at UC Berkeley suggests a glimmer of hope when it comes to the thorny problem of recycling plastics — one that may allow us to have our cake, and potentially take a very small bite, too.
The group has devised a catalytic recycling process that breaks apart the chains of some of the more commonly used plastics — polyethylene and polypropylene — in such a way that the building blocks of those plastics can be used again. In some cases, with more than 90% efficiency.
The catalysts required for the reaction — sodium or tungsten — are readily available and inexpensive, they say, and early tests show the process is likely scalable at industrial levels. It uses no water and has fewer energy requirements than other recycling methods — and is even more efficient than manufacturing new, or so-called virgin, plastics, the researchers say.
“So by making one product or two products in very high yield and at much lower temperatures, we are using some energy, but significantly less energy than any other process that’s breaking down polyolefins or taking the petroleum resources and turning them into the monomers for polyolefins in the first place,” said John Hartwig, a UC Berkeley chemist who was a co-author of the study published recently in the journal Science.
Polyolefins are a family of thermoplastics that include polyethylene — the material used to make single-use and “reusable” plastic bags — and polypropylene — the ubiquitous plastic that holds our yogurts and forms microwaveable dishes and car bumpers. Polyolefins are produced by combining small chain links, or monomers, of ethylene or propylene, which are typically obtained from oil and natural gas.
Polyethylene and polypropylene account for the majority (57%) of all polymer resins produced, the study authors noted. They have proven a plague to the environment, and in microplastic form have been found in drinking water, beer and every organ in the human body, as well as blood, semen and breast milk.
Hartwig and R.J. Conk, a graduate student who led the research, said they have not yet heard from the plastics, recycling or waste industries. They said they had been keeping their technology under wraps until publishing their paper and obtaining a patent on the process.
A spokeswoman for the Plastics Industry Association declined to comment or provide an expert to review the paper.
Hartwig said there are some caveats to the work. For instance, the plastic has to be sorted before the process can be applied. If the products are contaminated with other plastics, such as PVC or polystyrene, the outcome isn’t good.
“We don’t have a way to bring those [plastics] back to monomer, and they also poison our catalyst,” said Hartwig. “So for us, and basically for everybody else, PVC is bad. It’s not able to be chemically recycled.”
He said other contaminates — food waste, dyes, adhesives, etc. — could also potentially cause problems. However, the researchers are still early in the process.
But plastic bags, such as the ones used to hold produce in supermarkets, offer promise as they are relatively clean and “nobody knows what to do with them.” He said plastic bags are problematic for material recovery facilities where they are known to gum up machinery.
“There are places that do collect those bags. I don’t know what they do with them. Nobody wants them,” he said.
But others are less sanguine.
Related Articles
Why some people enjoy pain-inducing and face-puckering foods
Would you consider cloning your pets?
Most Americans don’t trust AI-powered election information: survey
Billionaire, SpaceX employee crewmate make history with 1st commercial spacewalk
A baby in Gaza has a strain of polio linked to mistakes in eradication campaign, experts say
Neil Tangri, science and policy director at GAIA — an international environmental organization — said that while he was not a chemist or chemical engineer, and therefore couldn’t comment on the methods, he noted that there are broader “real world” issues that could prevent such a technology from taking off.
“Plastic recycling is not something we do well … we only get about 5% or 6% per year. So there’s a hunt for new technologies that will do better than that,” he said. “My basic warning is that going from small-batch analysis in the lab to functioning at scale with real-world conditions … it’s a huge, huge leap. So it’s not like we’re going to see this move into commercial production in the next year or two.”
He noted that while the reaction temperature cited was lower than that used in pyrolysis — the burning of plastic for fuel — or cracking — when plastics are made from virgin material — it still requires a lot of energy, and therefore potentially creates a fairly sizable carbon footprint. In addition, he said, 608 degrees — the reaction temperature cited — is the temperature “where dioxins like to form. So, that could be a challenge.” Dioxins are highly toxic byproducts of some industrial processes.
But, Tangri said, even if you could solve all of those issues — as well as the sorting and contamination issues Hartwig cited — “it is so cheap to make virgin plastic that the collection, the sorting, the cleaning … they were talking about … all of those steps, the energy use, you just can’t sell your [recycled material] at a price that makes sense to justify all that …. And that’s not really the fault of the technical approach. It’s the realities of the economics of plastic these days.”
It’s a point to which Lee Bell, technical and policy advisor for IPEN — a global environmental advocacy group — agrees.
“What appears promising in the lab rarely translates to commercial scale success and high yields from mixed plastic waste,” he said. “Not only do they have to deal with the diabolical issue of unavoidable plastic contamination [because chemical additives are in all plastic] but also competing with cheap virgin plastic in the marketplace.
“My view is that this is yet another lab experiment on plastic waste that will ultimately be thwarted by mixed plastic waste contamination and commercial realities,” he said.
©2024 Los Angeles Times. Visit at latimes.com. Distributed by Tribune Content Agency, LLC.